The LED lighting in the interior of the Nugget are also connected to the LIN bus. The standard LED option has four different LED strips each controlled by a physical ion/off switch and for all four strips there is a (physical) common up/down dimmer switch. Through the hidden service menu of the touch screen panel an additional LED menu can be added to the touch screen display. On this menu the LED intensity can be controlled like the hardware dimmer switches. Next to that the color tone (warm/cold light) can be controlled, however the standard LED strips are monochrome so it is of little use. On the LIN bus, the messages with ID=0x05 and 0x3B are associated to the LEDs. Looking at ID=0x05 there is one byte, the second byte of 8 that carries the settings information on Intensity and Tone:
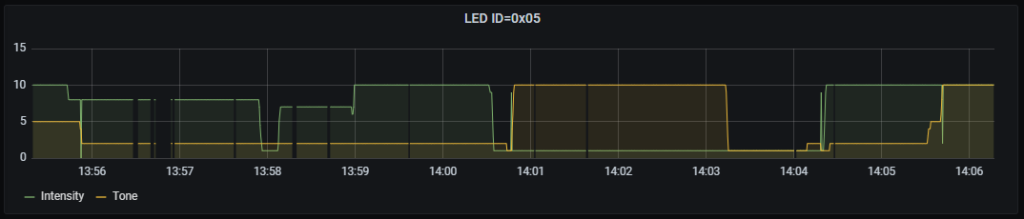
The Intensity and Tone can vary between 1-10. The first byte appears to contain some status bits explained below. The remaining bytes of the 8-byte message seem to always contain zeroes. The other message ID associated to the LED’s seems to replicate this information if the first two bytes but there are small differences:
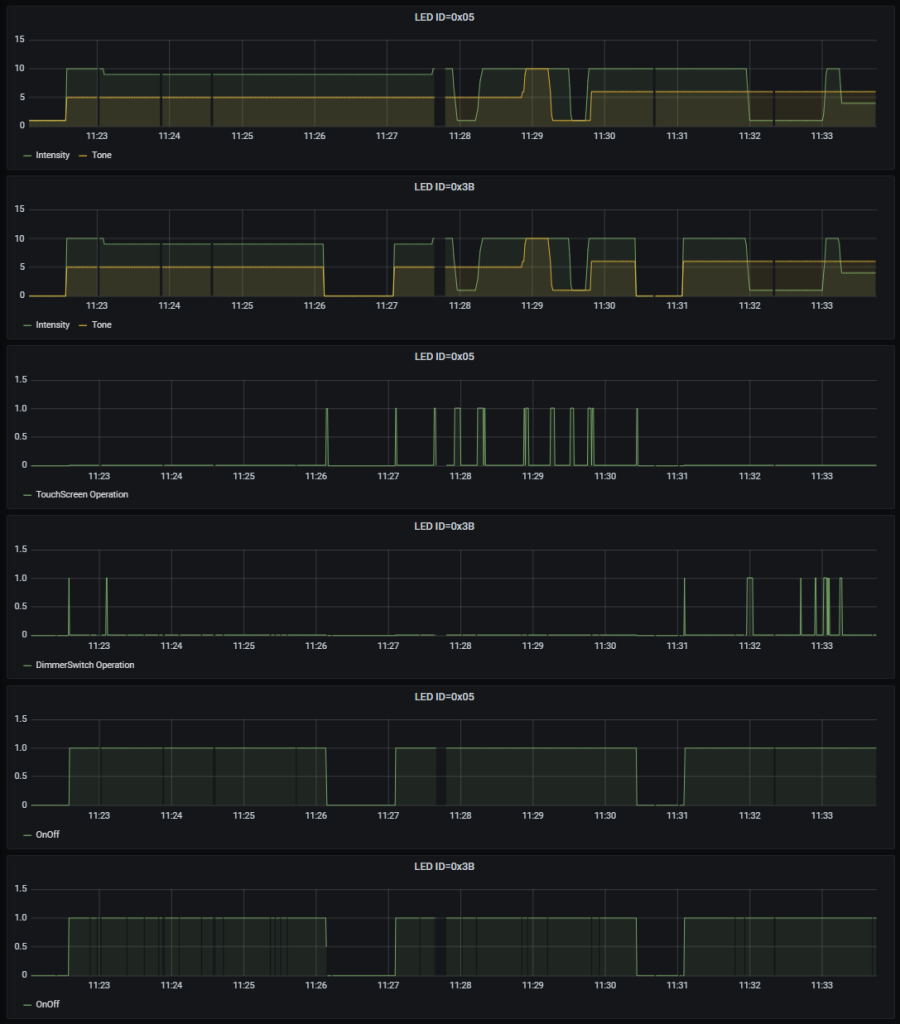
Bit 0 of Byte 0 of this message is zero when the LEDs are disabled or turn-off in the touch screen menu and right after turning on the 12V main switch. See the two bottom traces. When the LEDs are turned off form the touch screen, interestingly the message ID=0x05 still retains the Intensity/Tone settings, while in the 0x3B message those are both set to zero.
Bit 7 of Byte 0 is high when the Intensity or Tone are controlled as can be seen from the two middle traces. The message ID=0x05 has this bit high when it is touchscreen operated. While ID=0x3B has this bit high when it is operated from the physical dimmer buttons.
This last bit may have the purpose of notifying either the touchscreen or the LED controle module that settings of Intensity (and/or Tone) are being changed so that the other party can update the information accordingly. When the Dimmer switch is operated, the LED module sets bit 7 of byte 0 high in the response to a 0x3B header so that the touchscreen can update its Intensity. When the touch screen is operated to either change Intensity and Tone settings or the on/off button on the display is used, it sets this same bit high in the 0x05 message where the touchscreen most likely send both the header and the data part of the actuator-type LIN bus message.
The decoded protocol description is:
-------------------------------------------------------------------------------- LED lighting 1 ID : 0x05 data: 01 5A 00 00 00 00 00 00 | | | | | | | | AA | | | | | | | = b0: 1 = power on (touchscreen leading) | | | | | | | = b7: 1 = touchscreen operated TI | | | | | | = upper nibble: Color Tone T: 0-10 | | | | | | = lower nibble: Intensity I: 0-10 ?? | | | | | = (always 0x00) ?? | | | | = (always 0x00) ?? | | | = (always 0x00) ?? | | = (always 0x00) ?? | = (always 0x00) ?? = (always 0x00) -------------------------------------------------------------------------------- LED lighting 2 ID : 0x3B data: 01 5A 00 00 00 00 00 00 | | | | | | | | AA | | | | | | | = b0: 1 = power on (dimmerswitch leading) | | | | | | | = b7: 1 = dimmer switch (kitchen side) operated TI | | | | | | = upper nibble: Color Tone T: 0-10 | | | | | | = lower nibble: Intensity I: 0-10 ?? | | | | | = (always 0x00) ?? | | | | = (always 0x00) ?? | | | = (always 0x00) ?? | | = (always 0x00) ?? | = (always 0x00) ?? = (always 0x00) --------------------------------------------------------------------------------